Low emissivity glass, also known as low-E glass, has become a pivotal element in contemporary architecture and construction, owing to its energy-efficient properties and capacity to enhance comfort within buildings. Understanding the cost implications of low-E glass is essential for both industry professionals and homeowners considering its integration into their projects.
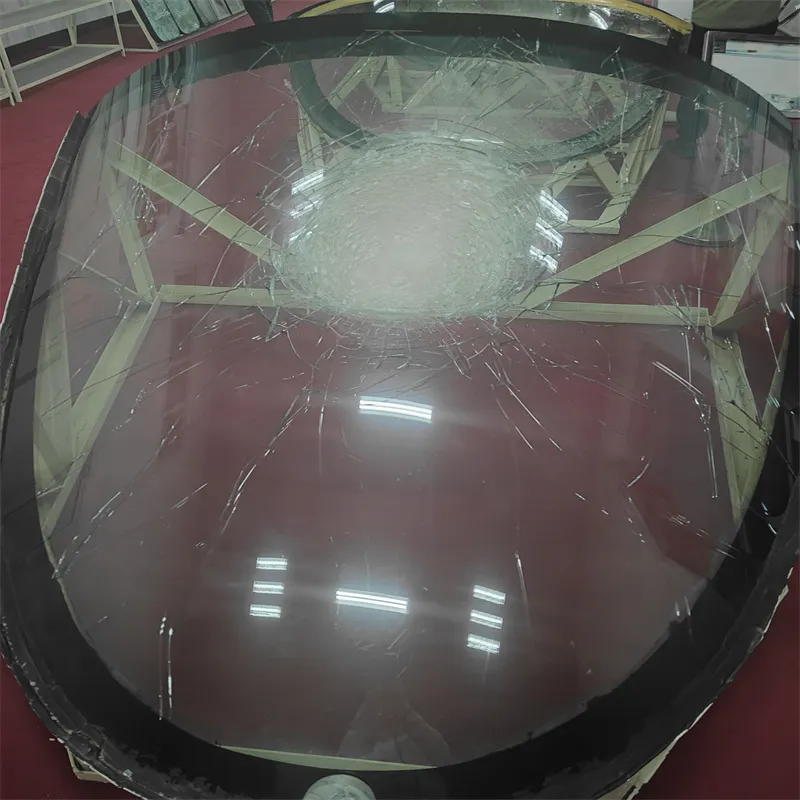
The primary advantage of low-E glass lies in its ability to reduce energy consumption by minimizing heat transfer. This is achieved through a microscopic coating that reflects infrared energy while allowing visible light to pass through. As a result, buildings equipped with low-E glass maintain a consistent internal temperature, thus reducing the need for additional heating or cooling.
When considering the cost of low-E glass, it’s crucial to weigh the initial investment against the long-term savings. The upfront cost of low-E glass is typically higher than that of standard glass. This is due to the specialized manufacturing process which involves the application of the low-E coating. Factors such as the type of coating, whether it’s soft coat or hard coat, can also influence the price. Soft coat low-E glass is generally more expensive due to its superior insulating properties and enhanced clarity.
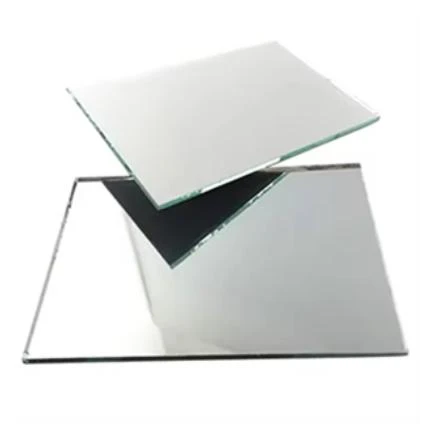
Despite the higher initial expenditure, low-E glass proves to be cost-effective over time. Studies have shown that buildings utilizing low-E glass report a significant reduction in energy bills, making it a highly sustainable option. The potential for reduced HVAC costs, backed by real-world experiences from various construction projects, highlights its economic viability. Moreover, the installation of low-E glass can substantially increase property value and appeal, a factor worth considering for those planning to sell their properties in the future.
low emissivity glass cost
Expert testimonials underscore the importance of selecting the right type of low-E glass, tailored to specific climate conditions and project needs. For colder climates, high-performance low-E glass with a higher solar heat gain coefficient (SHGC) is recommended to maximize passive solar gain. Alternatively, in warmer regions, a lower SHGC is preferred to minimize heat intake and reduce cooling costs.
Trustworthiness in sourcing low-E glass cannot be overstated. Engaging with reputable suppliers who provide quality guarantees and post-installation support ensures not only the longevity but also the optimal performance of the glass. Certification from recognized bodies such as the National Fenestration Rating Council (NFRC) serves as a reliable indicator of product quality.
Moreover, the expertise in installation plays a vital role in optimizing the benefits of low-E glass. Professional installation ensures proper sealing and alignment, preventing air leaks and maintaining the integrity of the thermal envelope. Experienced contractors bring a wealth of knowledge that can significantly impact the overall performance and energy efficiency of the glass.
In summary, while the cost of low-E glass may initially appear steep, its advantages in energy efficiency, coupled with its potential to enhance property value and provide aesthetic appeal, make it a worthwhile investment. By leveraging expert knowledge and opting for reliable suppliers, stakeholders can effectively balance cost considerations with the manifold benefits that low-E glass affords. As energy efficiency becomes an increasing priority, understanding the cost dynamics and long-term benefits of low-E glass remains crucial for making informed and sustainable building choices.